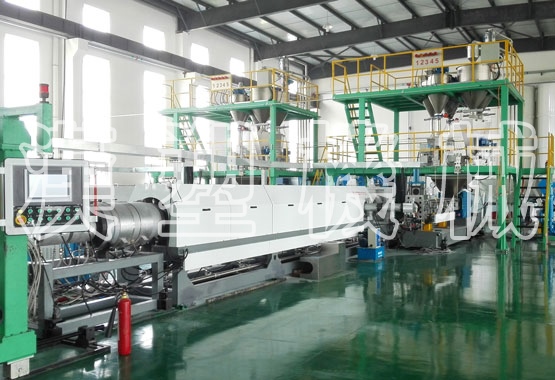
Introduction of XPS foam board production line
1.Focus on the manufacturing and technology research of complete sets of XPS foamed extrusion line
2.In China we master most advanced CO2 foaming technology for XPS extrusion line, can provide turn-key project solution for domestic and overseas customers.
3.Full automatic control of processing, with stable and efficient productions
Model disctription:
(S - means the 1st stage is single screw extruder, D - means the 1st stage is double screw extruder)
Main extruder | Screw diameter | Driving motor(kw) | Extrusion capacity | Range of product density(mm) | Thickness range of product(mm) |
S90/120 | 90/120 | 45/37 | 150-200 | 28-36 | 20-50 |
S135/150 | 135/150 | 75/55 | 300-400 | 28-36 | 20-100 |
S170/200 | 170/200 | 200/90 | 400-600 | 28-36 | 20-100 |
D65/120 | 65/120 | 45/37 | 150-200 | 28-36 | 20-50 |
D75/150 | 75/150 | 110/90 | 300-400 | 28-36 | 20-120 |
D85/200 | 85/200 | 132/90 | 500-700 | 28-36 | 20-150 |
D95/250 | 95/250 | 160/132 | 700-1000 | 28-36 | 20-150 |
Notes: (1st stage screw Recommend to use double-screw)
Advantage of adopting double-screw :compared with single screw used for 1st stage of extruder, the double screw has more capacity, stable working.
Equipment list
1.Material loading and feeding system (Germany brabenda for option)
2.1st stage of parallel double screw extruder
3.Foam agent injection system (Linde or Lewa for option )
4.Screen exchanger
5.2nd stage of single screw extruder
6.Static mixer
7.Die
8.Calibration unit
9.Haul-off unit
10.Cooling conveying roller
11.Edge cutter
12.Main Cross cutter
13.Electric control system ( ABB, SIEMENS, SCHNEIDER Brand)
Optional list
1.Surface planer and groover
2.Longitudinal groover (longitudinal trimming and shiplap, like SL,TG,RC)
3.Cross groover (cross trimming and shiplap)
4.Cooling and turning rack (vertical cooling tower )
5.Packaging machine
6.Automatic packing machine
7.Recyling machine